- sales.hk@pfc-device.com
- 852-2558-0181
Support
Contacts
Location
1/F., Shell Industrial Building, 12 Lee Chung Street, Chai Wan, Hong Kong.
Have Any Questions?
852-2558-0181
Email Us
sales.hk@pfc-device.com
New Product
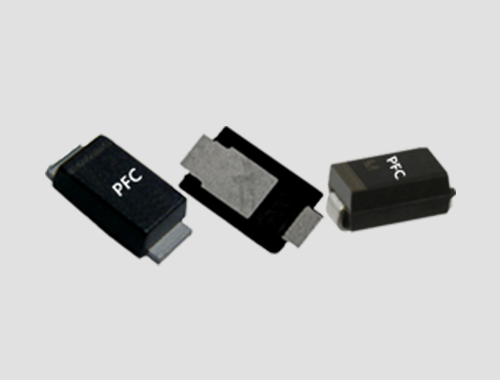
SMAF-A
PFC new development patterns SMAF-A package product for mobile phone charger and power supply applications Network & Communction need to develo...
1.Bending Terminal Leads
When bending the leads, in order to avoid excessive force in the area where the leads enter the plastic body,
use a tool clamps the point between the package and the bending point. Improper bending will damage the die,
resulting in a degradation in electrical characteristics or a reliability problem such as poor resistance to moisture.
There are some rules for the lead bending:
1. The leads should be securely clamped between the bending point and the plastic body. The recommended
minimum distance is shown as below:
X = 2 mm for DO-41, DO-15, Case.
X = 3 mm for DO-201AD Case.
X = 4 mm for R-6 Case.

2. Do not clamp on the plastic body, the forming tool should not damage the leads or the plastic body.
3. The leads must be bent only once and they should not be bent at an angle of more than 90℃
4. Leads must be formed before fixing them to a PCB or to a heatsink.
2.Mounting to Heatsink
The mounting surface of a heatsink should be free from foreign materials and metallic filings, and have enough
flatness and finish comparable to that of back of diode package. Don’t screw up the unit from backside ( heat sink )
and screwing up the unit from the front side (with marking). Be sure, when mounting devices to a heatsink,
that excessive torque may cause a mechanical failure of the device or a reliability problem.
( ex. electrical degrade…..). Also note, insufficient torque results in poorer heat transmission.
Recommended mounting hole, screw and mounting torque corresponding to our package are shown in Table.

Thermal compounds ( greases ) facilitate interface thermal conduction between device and heatsink.
Recommended compounds are hydrophilic oil based. When applied, compounds should be spread evenly
in a very thin layer over the whole contact area.
The contact thermal resistance Rthj-c in our datasheet are defined with the recommended mounting torque
and with the thermal compound.
3.Soldering of Through-hole Mounting Device
Resistance to soldering heat test is carried out under the condition shown below. Soldering should be
completed at a lowest possible temperature for a shortest period.
Temp. = 260 ℃(max)
Duration = 10 sec (max)
Fig.-02 Shows the Dip duration vs. Solder Temperature Rating for plastic diodes.
General requirements for manual soldering are as follows:
1. Use a soldering iron for 40 watts maximum, that is grounded or with a high insulation resistance.
2. The iron tip is kept away from any plastic body.
3. Attachment should be achieved in not more than 3 seconds.
Be sure again not to put an excessive mechanical stress on device, as a rough insertion of device into
a through-hole, or manual reforming of leads after soldering.
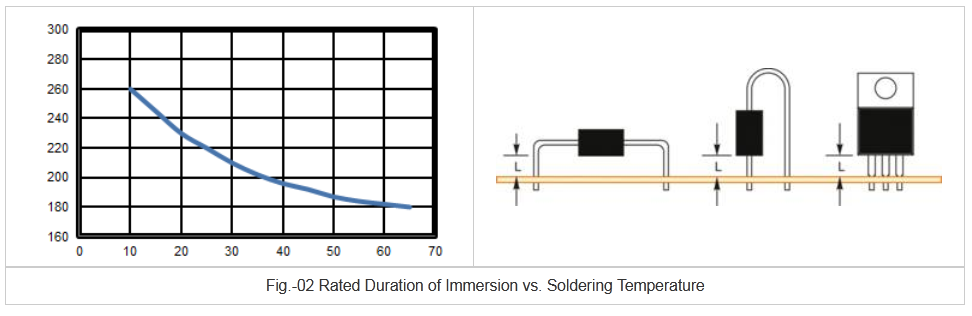
4. Suggested thermal profiles for soldering process
4.1.Reflow profiles of surface-mount device
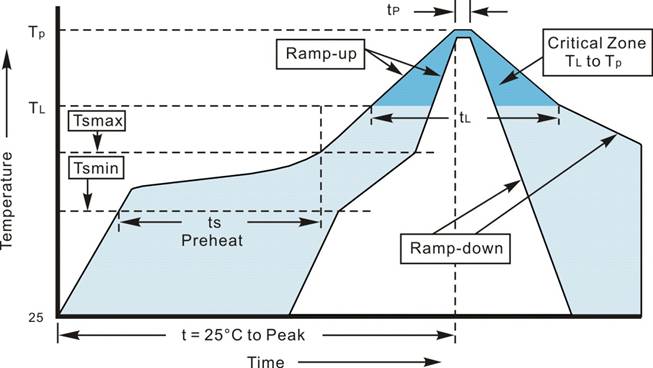
Reflow Profiles in tabular form
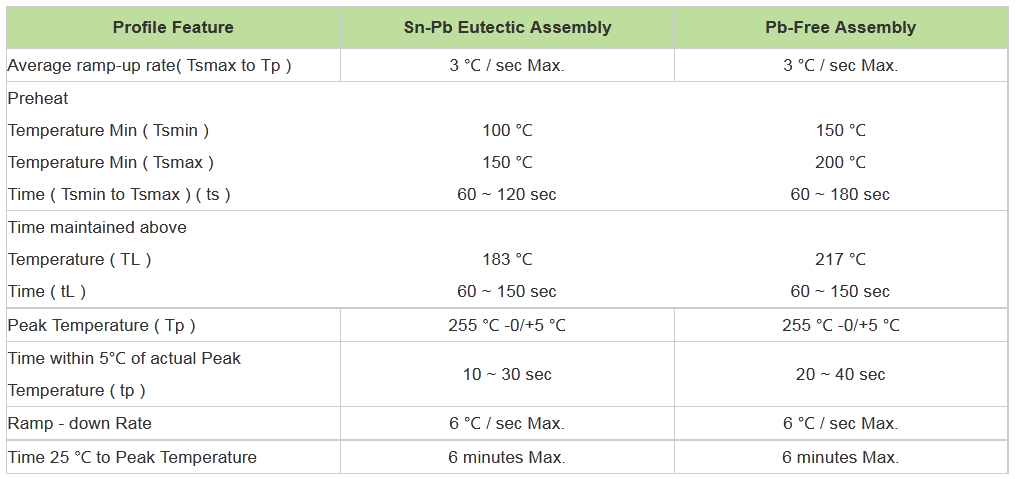
4.2.Wave profiles of DIP device
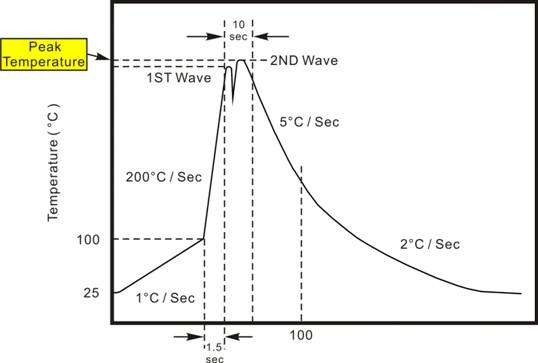
Wave Profiles in tabular form
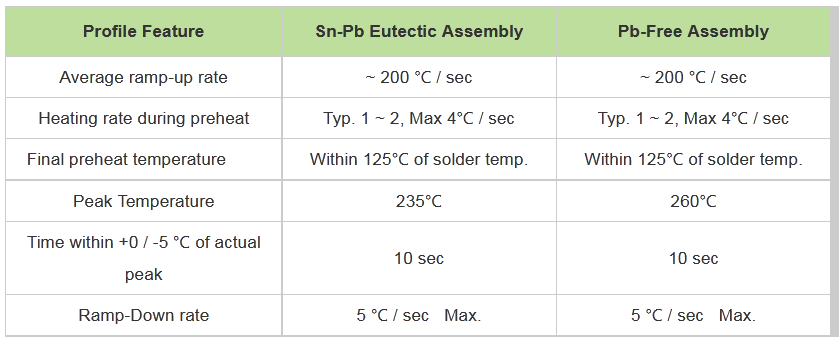
5. Recommanded Warehouse Storage conditions:
Ensure that electrical product may be stored for extended periods before use, we recommend that warehouse storage condition as:
Temperature = 5℃ ~ 30℃
Humidity = 45 ± 25%